中國冶金報 中國鋼鐵新聞網
記者 樊三彩 報道
記者 朱亞明 通訊員 譚承溫 攝影
“湛江鋼鐵已制定2025年能效達標桿行動計劃,未來將依托鋼協‘雙碳最佳實踐能效標桿示范廠’培育平臺,推動能效達標桿工作進一步深化。”在12月9日召開的鋼鐵行業能效標桿三年行動方案現場啟動會上,寶鋼湛江鋼鐵有限公司黨委書記、董事長、總指揮劉代德表示。
劉代德在會上分享了湛江鋼鐵追求極致能效、實現標桿能耗的系列工作舉措及發展規劃。他表示,2017年底,湛江鋼鐵實現達產、達標、達效、達耗的“四達”目標,創造了國內大型鋼廠從投產到年度“四達”的最快紀錄。以此為基礎,湛江鋼鐵率先實現“廢氣超低排、廢水零排放、固廢不出廠”,率先實施低碳冶金技術,能源系統具有穩定可靠、加工轉換效率高、余能回收利用率高、水資源循環利用率高等優勢。
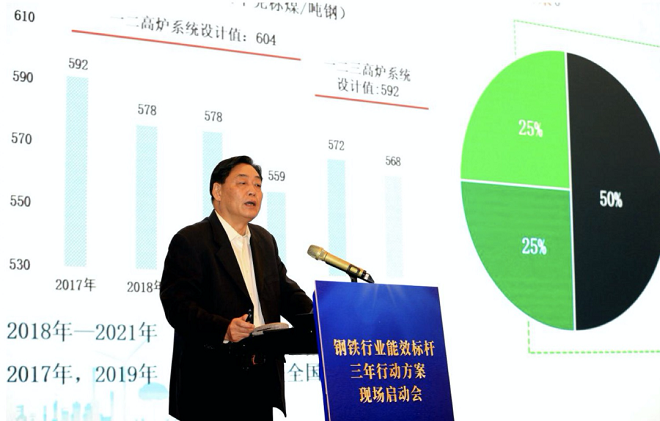
圖為劉代德作《追求極致能效、實現標桿能耗,打造綠色低碳高質量示范基地》報告
5年累計節能110萬噸標煤
“5年來,湛鋼噸鋼綜合能耗逐年下降,2022年較2017年(全面達產年)下降24千克標煤/噸鋼,年節能36萬噸標煤,5年累計節能110萬噸標煤。”劉代德總結了湛江鋼鐵自2017年以來的節能工作成效。
其中,湛江鋼鐵通過優化生產運行、減少界面溫降、提高工序用能效率,累計節能9萬噸標煤;通過優化能源系統,減少放散放損,提高能源轉換效率,累計節能9萬噸標煤;通過實施38項節能技改項目,年節能約18萬噸標煤。
劉代德介紹,5年來,為追求極致能效,湛江鋼鐵共采用國際先進節能環保技術約116項,噸鋼投資720元,同時采取了一系列工作舉措。
提升加工轉換效率。一是通過系統優化,減少能源介質放損。2022年,湛江鋼鐵BFG(高爐煤氣)放散率較2017年下降7.6%,同比年減少煤氣放散13.9億標準立方米;2022年低壓蒸汽放損率較2019年下降28%,同比年減少蒸汽損失10.1萬噸。二是提升余能回收效率,應收盡收。2022年,湛江鋼鐵噸鋼蒸汽回收量、LDG回收量較2017年分別上升33.0%、24.7%,同比年增加蒸汽回收量174萬噸、LDG回收量2.75億標準立方米。三是提升海水淡化和壓縮空氣系統能效。2022年,湛江鋼鐵海淡系統蒸汽電耗、壓縮空氣系統電耗較2017年分別下降4%、19.5%,同比年減少蒸汽耗量2.4萬噸、年減少用電量8508萬kWh。四是提升發電系統能源效率。2022年煤電系統供電煤耗較2017年下降3克標煤/kWh,同比年減少用煤量16296噸動力煤;CDQ余熱發電率較2017年上升24kWh/噸焦,同比年增加發電量6298萬kWh。五是提升廢水回收量,降低噸鋼耗水。“湛江鋼鐵通過‘取-制-供-用-回’全系統管理和技術創新,廢水回收逐年增加,噸鋼耗水逐年降低,2022年較2017年下降1.35噸/噸鋼,年節水1720萬噸。”劉代德表示。
優化提升界面能效。湛江鋼鐵一方面提升魚雷罐車(TPC)周轉率,降低鐵水溫降。2022年TPC周轉率較2017年提升1.3次/日,鐵水溫降較2017年優化9℃,尤其2022年11月首次實現月度“破百”,達到98.9℃的歷史最好水平。另一方面提升軋鋼工序熱送熱裝比例。2022年熱軋工序熱裝熱送率(400℃以上)較2017年提升37個百分點,燃耗降低11%;2022年厚板工序熱裝熱送率(400℃以上)較2017年提升76個百分點,燃耗降低20%。“這兩項均創歷史最好水平。”劉代德強調。
大力推進智慧能源。一是開發智慧能源管理系統,實現能源管理四個轉變(從結果到過程、從指標到成本、從定性到定量、從業務到全員)。湛江鋼鐵研發國內首個基于“三流一態”(能源流、制造流、價值流、設備狀態)的智慧能源管理系統,開發出包含能耗日管控分析、成本分析、碳排放分析等451項功能頁面開發應用,實現能源管理四個轉變。同時,通過研發智慧能源在線調度決策平臺,實現能源系統在線預測與精準調控。二是開發應用智慧水控系統,實現全廠水系統管控四個統一(統一生產協同平臺、開放應用平臺、數據平臺、硬件平臺)。“2019年投運以來,噸鋼耗水下降40%。”劉代德指出。
應用節能技術。湛江鋼鐵加大投入,2017年以來實施了焦燒區域余熱資源綜合效能提升等38項節能技術改造,實現年節能量達18萬噸標煤。其中,通過余熱資源利用和設備能效提升分別實現節能45%、34%,貢獻率近80%。
煉焦、燒結、轉爐工序已穩定達能效標桿值
“目前,湛江鋼鐵煉焦、燒結、轉爐工序均已穩定達到能效標桿值,軋鋼工序能耗均優于寶鋼股份領航值。”劉代德說。
劉代德表示,為推動能效達標桿,湛江鋼鐵開展了體系化推進冶煉工序“達標桿”、軋鋼工序“創領航”行動。湛江鋼鐵將能效達標桿納入碳中和委員會推進體系,策劃實施能效達標桿勞動競賽,同時開展“達標桿”“創領航”案例發布,在企業營造良好推進氛圍。
在各工序上,湛江鋼鐵也多點發力,效果顯著。通過優化配煤穩定成焦率、提高CDQ蒸汽回收率、穩定焦爐煤氣及化產品回收率等措施,實現煉焦工序能耗(104kgce/t焦)穩定達標桿,較標桿值低6kgce/t焦;通過堅持低碳厚料層燒結、提高燒結余熱回收蒸汽等達先進值推進措施,燒結工序能耗(42.4kgce/t礦)穩定達先進,較標桿值低2.6kgce/t礦;通過調整轉爐煤氣回收參數、穿插式除塵風機降速節電等2022年達標桿推進措施,轉爐工序能耗(-31.4kgce/t鋼)穩定達標桿,較標桿值低1.1kgce/t鋼。同時,湛江鋼鐵通過提升熱裝熱送率、品種鋼加熱工藝優化、退火機組清洗段低溫堿洗應用等措施,使得熱軋工序能耗為39.4kgce/t,優于寶鋼股份的43.0kgce/t;酸軋工序、連退工序能耗分別為15.2kgce/t、45.6kgce/t,優于寶鋼股份的16.0kgce/t、47.0kgce/t等。
“高爐工序能耗未達標桿值,還需攻關。”劉代德強調,2022年高爐經濟爐料使用比例上升,焦比、燃料比劣化明顯;雖熱風爐燃耗、TRT發電效率有進步,較標桿值還有10kgce/t鐵的差距。
“根據湛江鋼鐵的發展計劃,到2025年,焦爐工序、轉爐工序將在達標桿基礎上,進一步提高能效水平,分別達到102kgce/t焦、-32.0kgce/t鋼的能耗水平。高爐工序通過熱風爐自動燒爐模型、高爐爐渣余熱回收等節能技術攻關,力爭能耗穩定達到標桿值。”劉代德說。
多管齊下打造能效標桿示范
劉代德表示,“十四五”期間,湛江鋼鐵將認真落實寶武集團要求,以極致能效為目標,快速實現標桿能耗,將湛江鋼鐵進一步打造成為綠色低碳高質量發展的能效標桿示范,向著“能效最高、排放最低、環境最優、社企和諧,具有國際領先水平的美麗湛鋼”目標堅定前行。
一是追求極致能效。2022年,湛江鋼鐵開展了能源管理師培訓及現場節能診斷,讓聽得見“炮聲”的人管現場能源,夯實極致能效推進基礎。“未來,湛江鋼鐵將穩步推進‘十四五’能效提升規劃。”劉代德介紹,湛江鋼鐵“十四五”能效提升規劃(包括256項節能項目,其中管理節能措施170項,節能改造項目86項)計劃總投資約12.7億元,預計節能量約26萬噸標煤/年,減少二氧化碳排放約68萬噸/年。2021-2022年已立項25個節能改造項目,累計節能量10.5萬噸標煤/年。
二是加快綠色能源開發。“2021年—2025年,湛江鋼鐵規劃新建廠區新能源裝機容量200兆瓦。”劉代德表示。據介紹,目前1期已并網,裝機容量48兆瓦,年發電量5700萬度;2期處于施工階段,計劃今年底投運,裝機容量47兆瓦,年發電量5300萬度;3期處于規劃階段,2025年前計劃累計完成光伏裝機容量150兆瓦和風電50兆瓦。
三是落實低碳冶金項目建設。“湛江鋼鐵未來將建設全國首套100萬噸的氫基豎爐系統工程,進一步開展‘氫基豎爐+電爐’短流程零碳鋼示范線項目研究、推進,實現噸鋼綜合能耗較傳統全流程下降38%。”劉代德表示,將力爭到2025年,豎爐穩定生產、達產年產量100萬噸,實現不同工況生產的靈活切換。